Finite elment modelling of fibre-epoxy resin microbond test
Here an axisymmetric 2D model of the microdroplet-fibre-stopper blade was made using ABAQUS/CAE.
Detailed results available here [click]
Results for blade at position 0 [click]
Results for blade at position 2 [click]
Results for blade at position 3 [click]
Results for blade at position 4 [click]
Results when maximum separation was defined as crterion for failure [click]
A Python script was prepared for permitting the automatic building of the FEM.
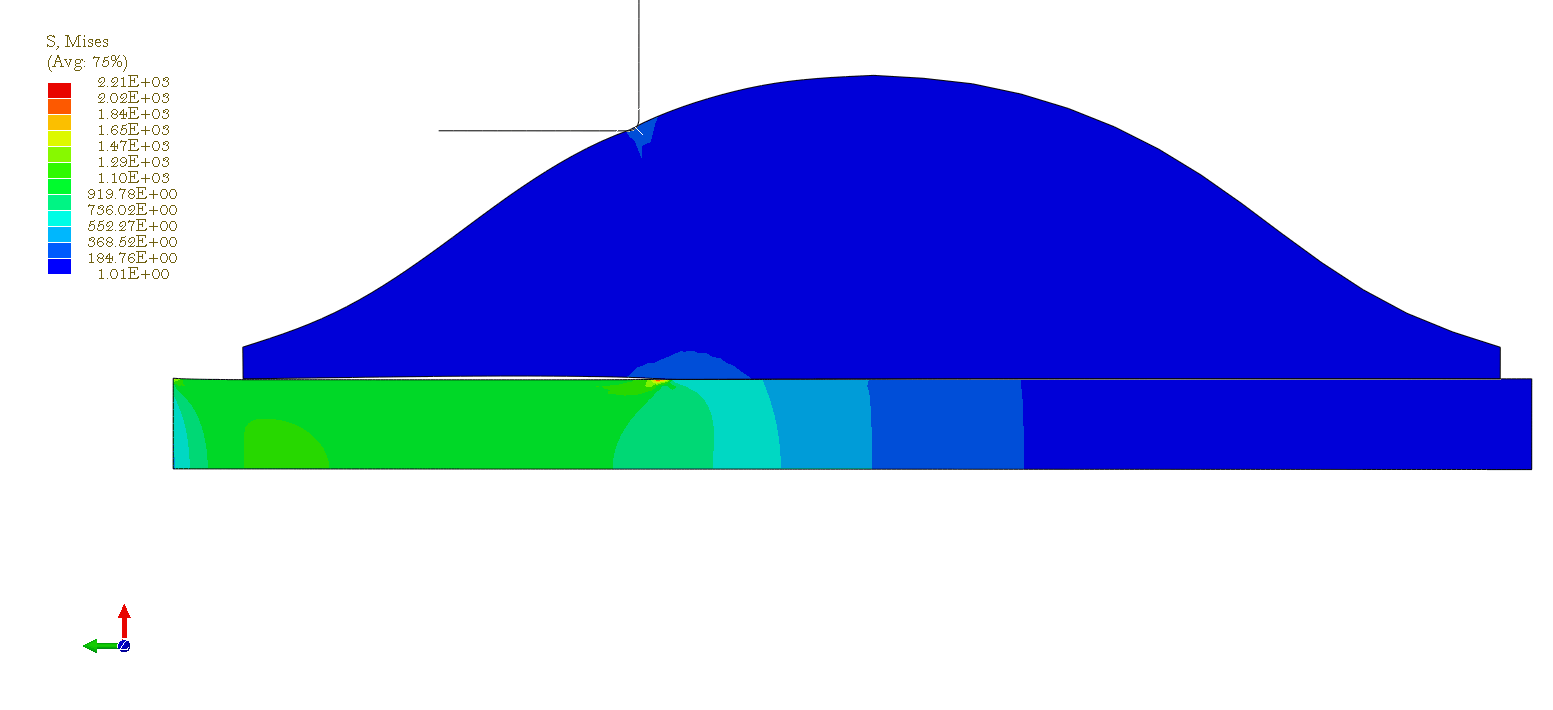
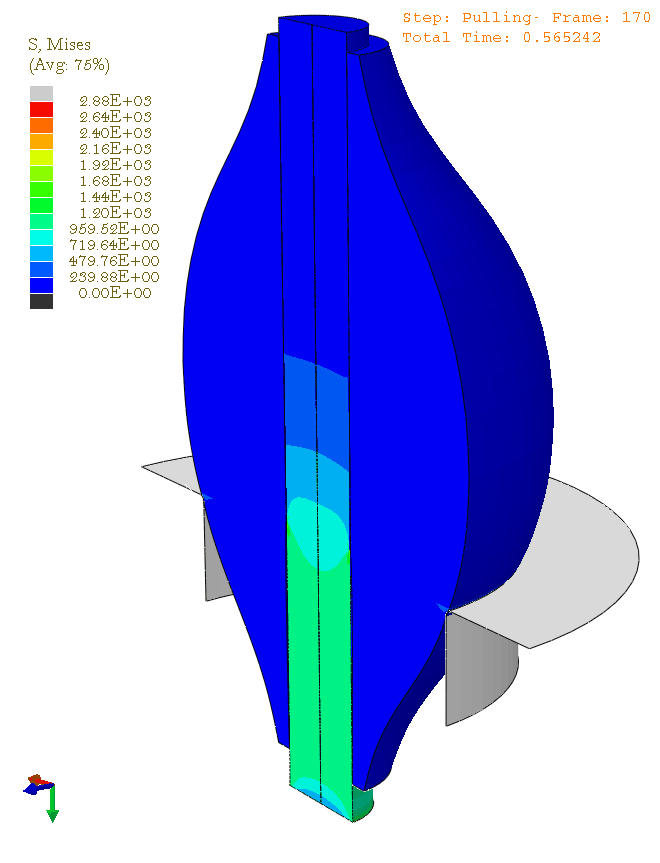
Finite Element Modelling
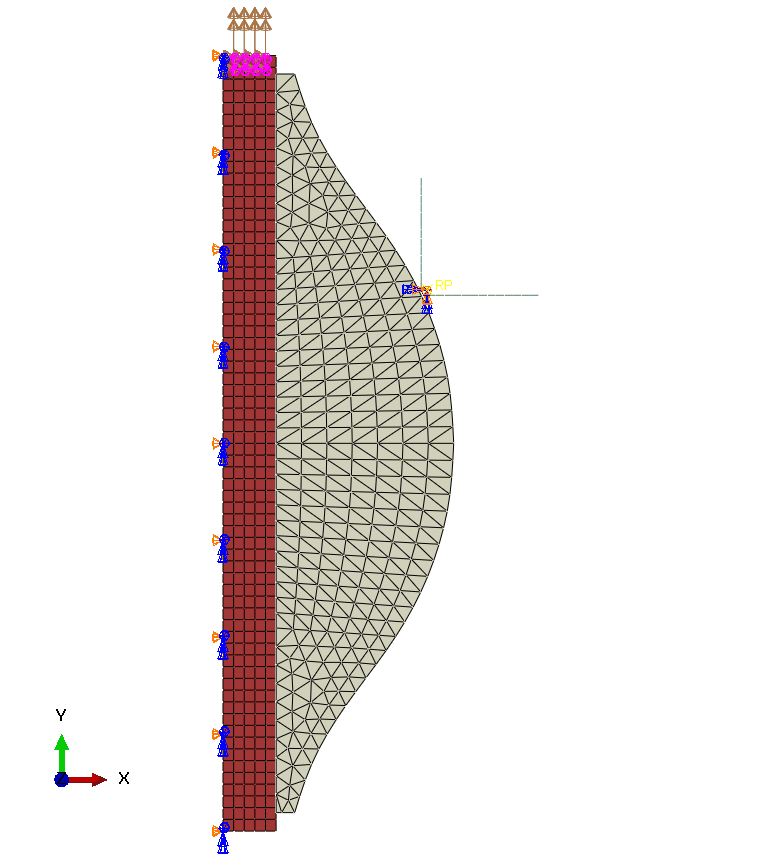
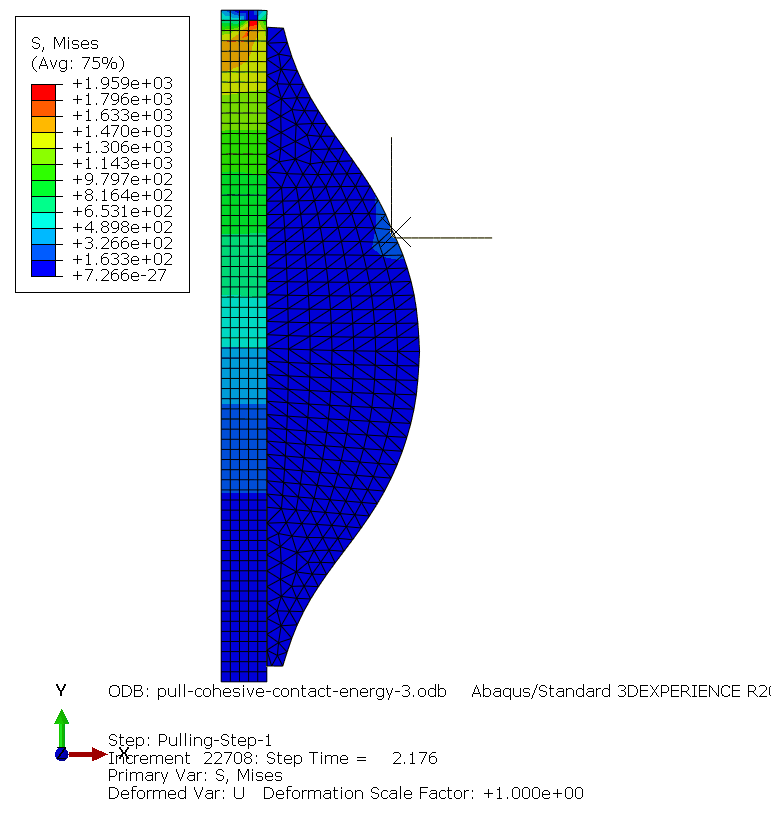
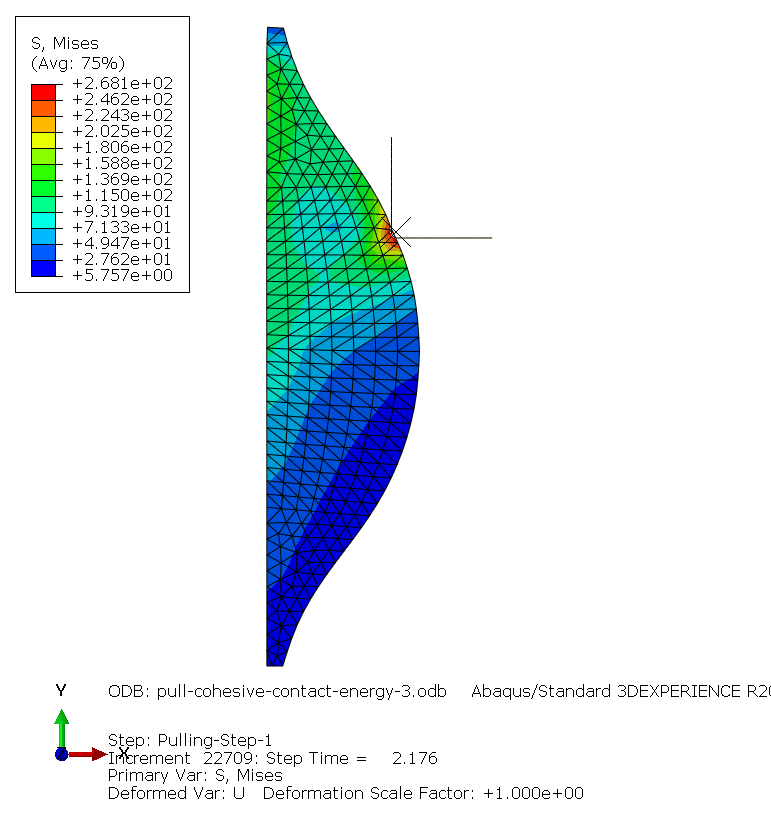
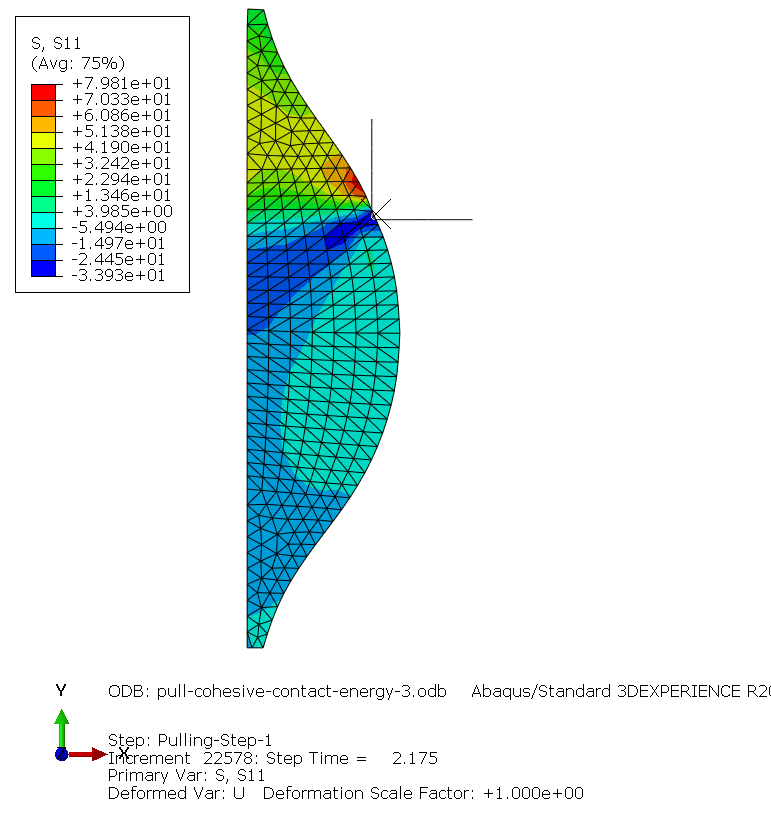
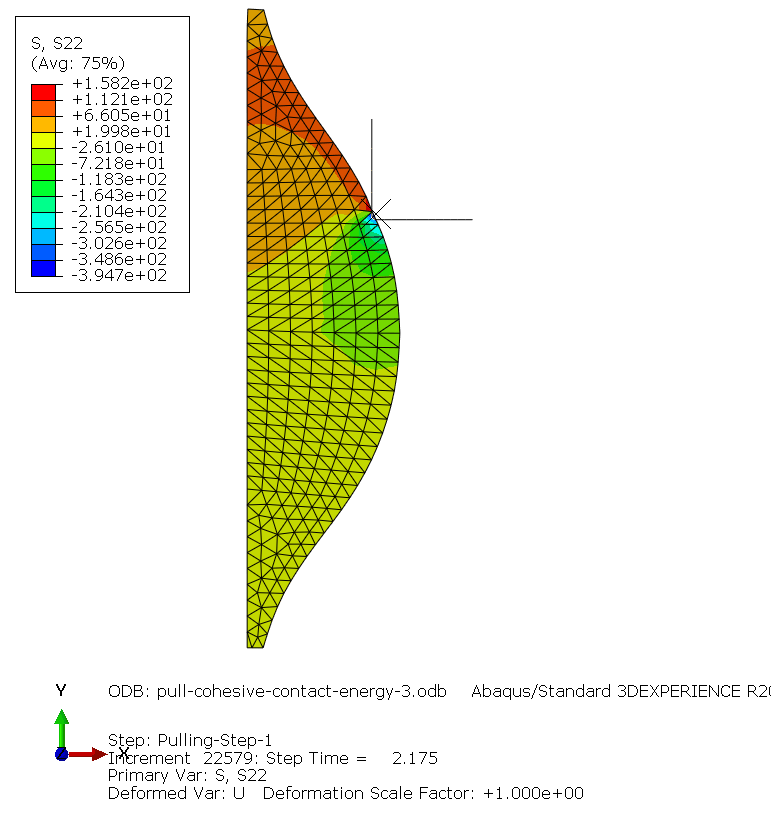
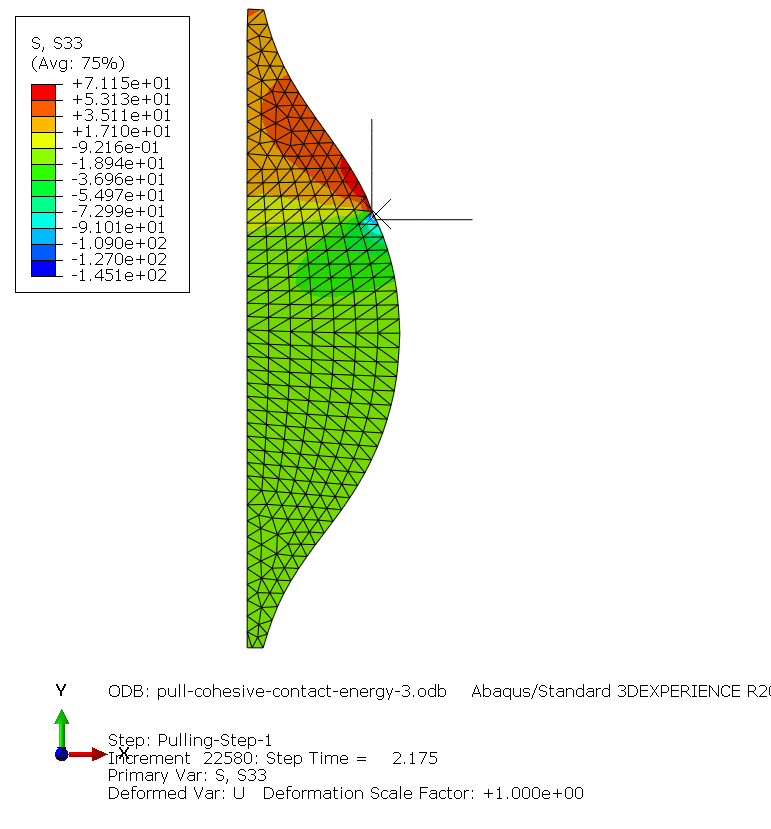
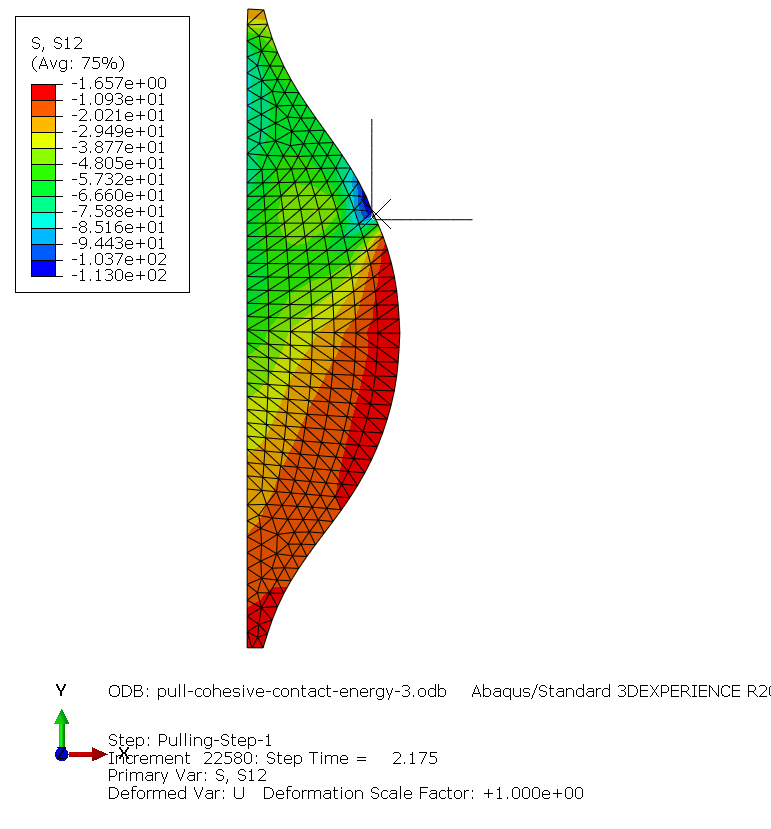
Damage model
Maximum nominal shear stress [Shear-1 Only] for damage initiation was 100 MPa. Normal Only and Shear-2 Only did not affect the results.
Alternatively a shear seperation of 1.2E-07 mm as separation at damage initiation, also gave the same result
Load v deformation data

Experimental data
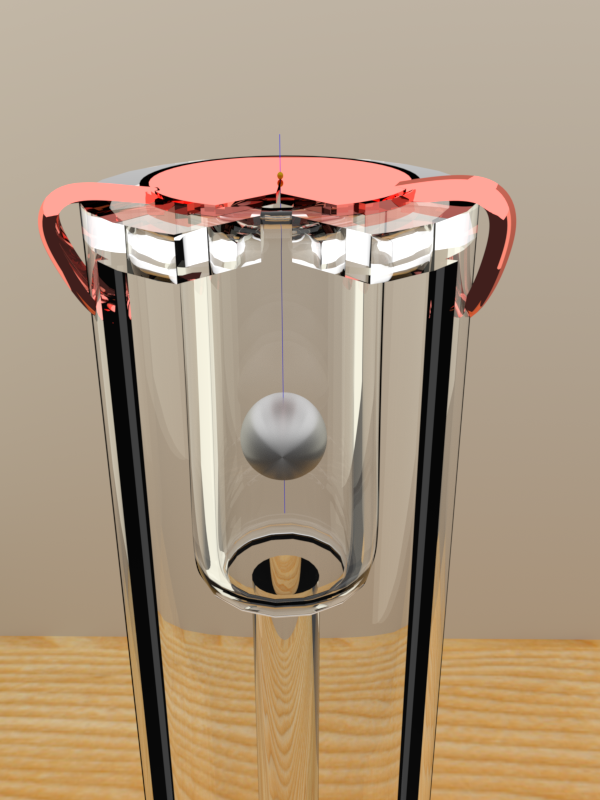
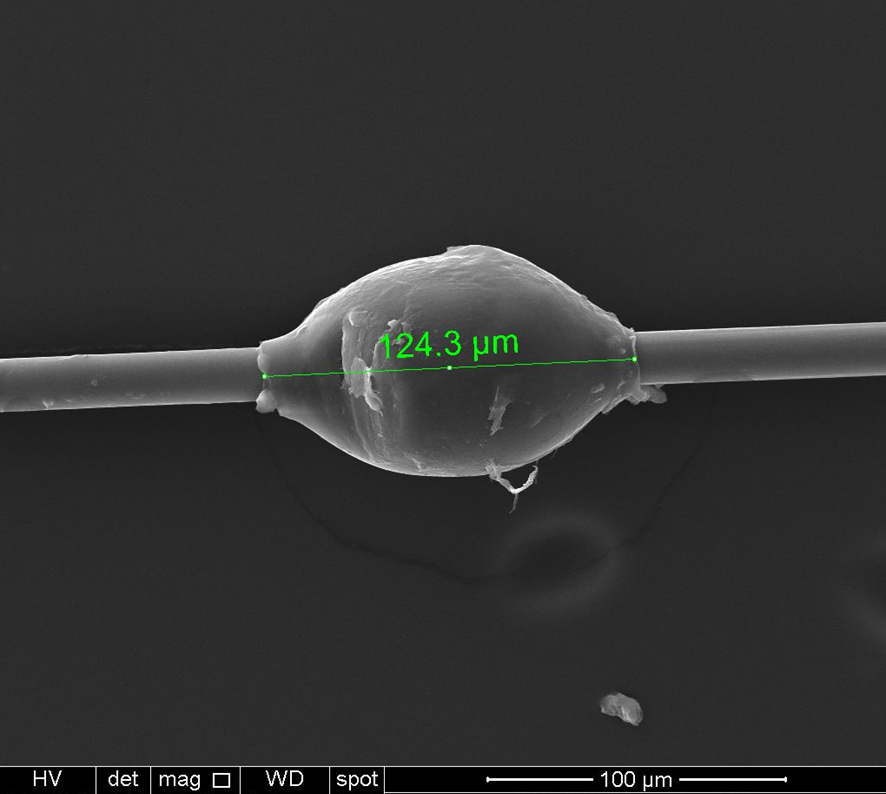
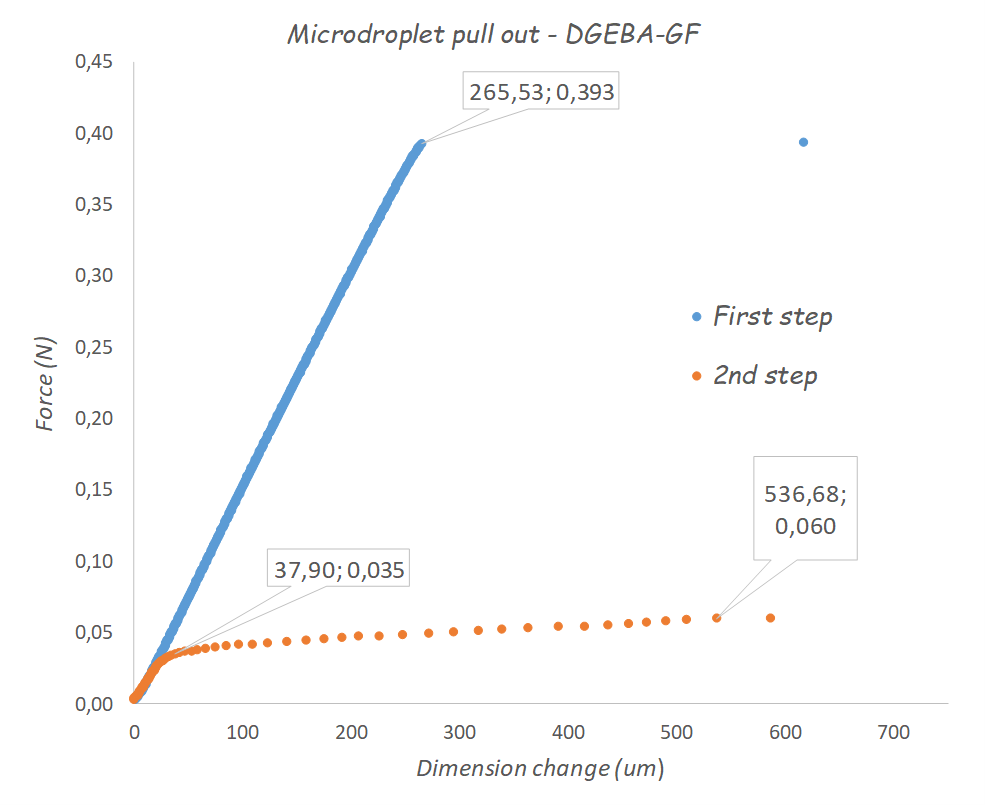
Notes:
Comparing the deflection values in the figure above with the droplet dimensions (i.e. 150 micron) shows that the deflection has continued uniformly for more than twice the size of the fibre-droplet interface.
A possible explanation could be that the there is some milimeters of the fibre attached to the fibre-droplet assembly as shown in the first figure above. And the measured large deflection is mostly the elongation of that piece of fibre. This kind of larger than expected deformations have been also reported previously in other works.
Elongation of the fibre
Given the fomula for tensile elongation: , and the values from the fisrt step of the experiment:
Load at the maximum displament, P = 0.393 N,
Length of the fibre, L = 17.64 mm
Fibre diameter, d = 0.0120 mm , or fibre section area: A = 0.0001131 mm2
Maximum recorded displacement, δL = 0.265 mm
would give: E ≅ 230 GPa.
Thus, the Young's modulus of the fibre should not be smaller than 230 GPa. Because lower values would mean that the deformation due to the elongation in the fibre alone will exceed the total displacement of 265 micron.
Counterpoint
The load is transferred from the fiber to the droplet by shear:
By considering the constraint the effective resistant section is the base of the droplet (ring shaped), then I would evaluate the stiffness of the system as compliant to those of the polymer 2,4-2,8 GPa (w is sligthly lower than droplet length 120-130um)
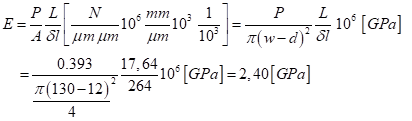
the elastic modulus of E-glass fiber is 70-75 GPa
Shear stress in the droplet-fibre bond
Shear stress in the interface: :
Therefore shear stress at the interface is calculated as: 83.43 [MPa]